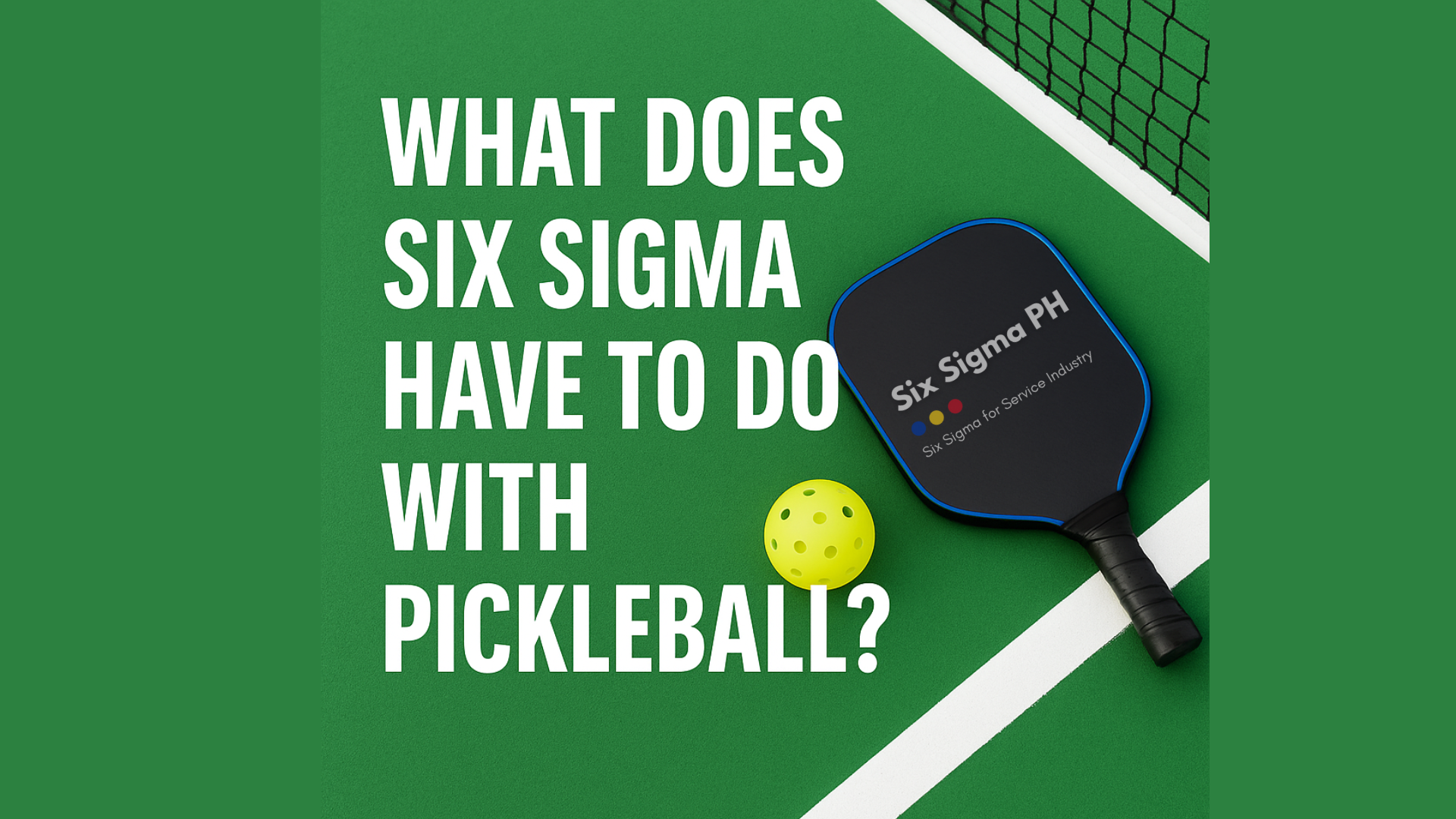
What Does Six Sigma Have to Do with Pickleball?
What Does Six Sigma Have to Do with Pickleball?
At first glance, Six Sigma—a methodology used to improve processes and reduce defects in businesses—and pickleball, one of the fastest-growing sports worldwide, might seem unrelated. But if you look closer, the connection is surprisingly strong.

I Slipped and Fell Into Six Sigma: Now What?
I Slipped and Fell Into Six Sigma: Now What?

Where to Find Your Lean Six Sigma Project: 5 Sources
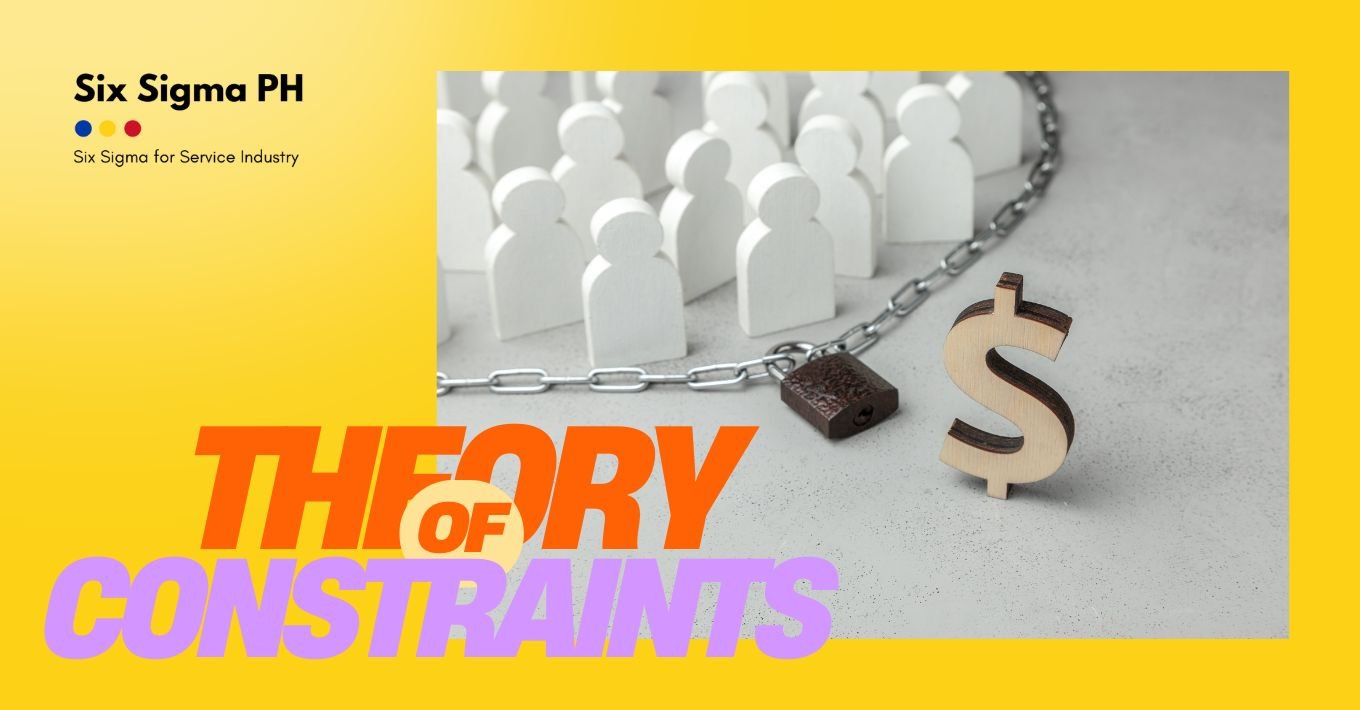
Five Simple Questions to Apply the Theory of Constraints (TOC) and Achieve Maximum Performance
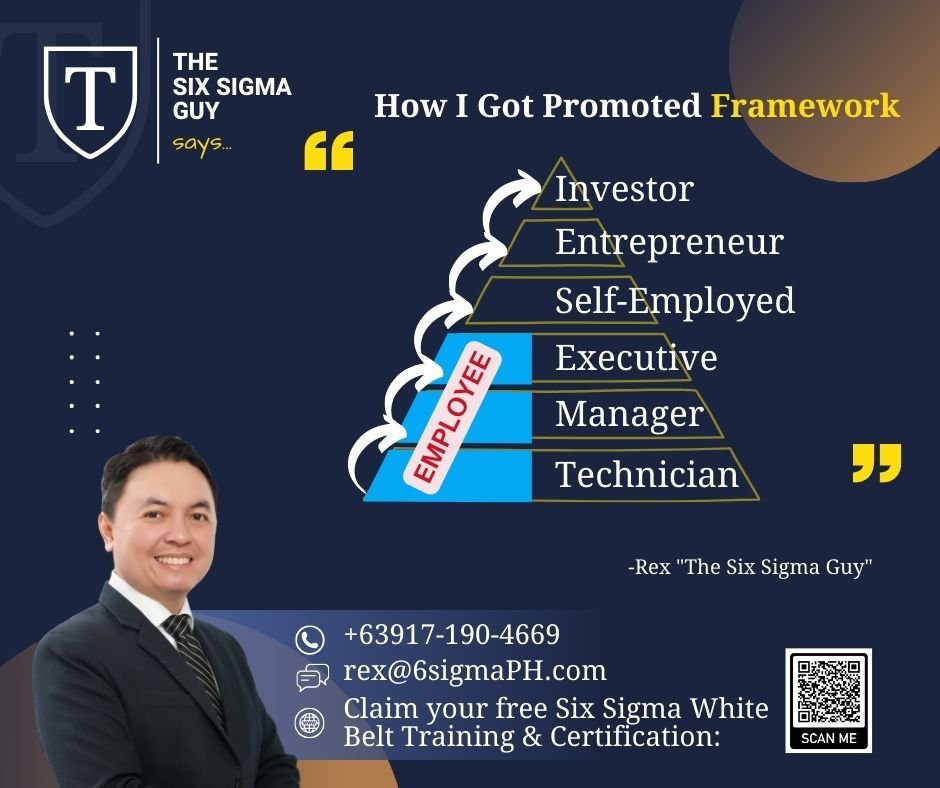
𝗛𝗼𝘄-𝗜-𝗚𝗼𝘁-𝗣𝗿𝗼𝗺𝗼𝘁𝗲𝗱 𝗙𝗿𝗮𝗺𝗲𝘄𝗼𝗿𝗸

𝐏𝐫𝐨𝐜𝐞𝐬𝐬 𝐄𝐱𝐜𝐞𝐥𝐥𝐞𝐧𝐜𝐞 𝐭𝐡𝐫𝐨𝐮𝐠𝐡 𝐋𝐞𝐚𝐧 𝐒𝐢𝐱 𝐒𝐢𝐠𝐦𝐚
𝐏𝐫𝐨𝐜𝐞𝐬𝐬 𝐄𝐱𝐜𝐞𝐥𝐥𝐞𝐧𝐜𝐞 𝐭𝐡𝐫𝐨𝐮𝐠𝐡 𝐋𝐞𝐚𝐧 𝐒𝐢𝐱 𝐒𝐢𝐠𝐦𝐚

Japan’s Omotenashi #1: The Art of Delivery Amazing Customer Experience
𝗪𝗵𝗮𝘁 𝗶𝘀 𝗢𝗺𝗼𝘁𝗲𝗻𝗮𝘀𝗵𝗶?
✅Omotenashi originated from the tea ceremony and is the Japanese way of providing guests with the best possible service and experience.
✅Omotenashi is not just about being polite or courteous but about anticipating the needs and preferences of the customers, exceeding their expectations, and creating a memorable and emotional connection with them.

The Curious Case of Being an ‘Accidental Project Manager’ with Michaela Teng
The Curious Case of Being an ‘Accidental Project Manager’ with Michaela Teng

The Six Sigma Guy Says
The Six Sigma Guy Says
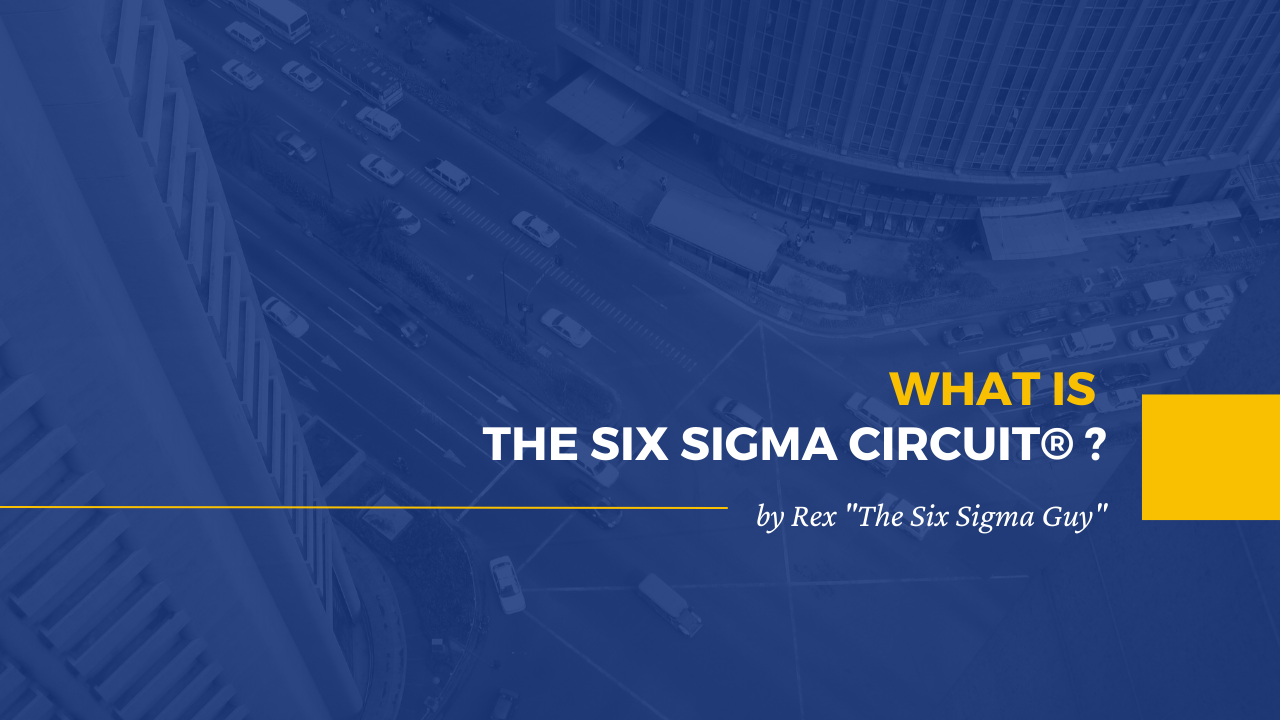
What is the Six Sigma Circuit?
What is the Six Sigma Circuit?

5 Recommended Books by Black Belt Certified, Jen Amar
5 Recommended Books by Black Belt Certified, Jen Amar

6 Recommended Books by Six Sigma PH’s Marketer
6 Recommended Books by Six Sigma PH’s Marketer

7 Recommended Books By The Scrum Coach
7 Recommended Books By The Scrum Coach

The Benefits of Lean Six Sigma in Hospitality and Tourism Industry
The Benefits of Lean Six Sigma in Hospitality and Tourism Industry